Двухкомпонентные полиуретановые покрытия для труб
25.05.2013
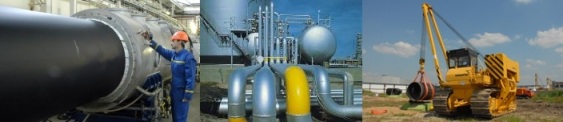
Жесткие полиуретановые лакокрасочные покрытия для защиты подземных или подводных трубопроводов
Уже в течение многих лет двухкомпонентные полиуретановые (2К ПУ) системы без растворителей отлично зарекомендовали себя в качестве подходящих систем для защиты труб. Этот класс продуктов охватывает полиолы в сочетании с полиизоцианатами и/или преполимерами. Благодаря их особым свойствам 2К ПУ системы предпочитают там, где требования высокого качества и долговечности сочетаются с жесткими условиями эксплуатации трубопроводов и резервуаров (например, нанесение в полевых условиях, высокие температуры эксплуатации, высокая концентрация солей, влажный грунт и т.д.).
Жидкие полиуретановые системы приобретают все большее значение в качестве наружных покрытий для нефтегазовых трубопроводов. Как в строительстве новых трубопроводов, так и при эксплуатации существующих используются системы для наружной окраски на основе ароматических изоцианатов и/или преполимеров. Основные требования, предъявляемые к окраске практически всех видов труб, — быстрое и надежное отверждение покрытия и исключительные физико-механические свойства, особенно в жестких окружающих условиях.
По результатам обмена опытом со многими экспертами в нефтегазовой области был составлен модифицированный профиль свойств сырьевых компонентов, соответствующий требованиям рынка. Скрининг тестовых систем в лаборатории дал очень хорошие результаты. Испытания были смоделированы таким образом, чтобы соответствовать типичным условиям климата в ближневосточном регионе. Одним из этапов оценочного процесса стали эксперименты по полевому нанесению; через 15 месяцев эксплуатации в условиях влажного грунта покрытие все еще находилось в отличном состоянии.
В настоящей статье представлены новые сырьевые компоненты жестких 2К ПУ систем для наружной окраски труб.
Преимущества стандартных 2Л ПУ покрытий для труб
2К ПУ системы уже десятилетиями признаны подходящими системами для защиты трубопроводов. Такие продукты используются для окраски новых труб (из стали или чугуна), а также для полевой окраски стыков.Для ремонта нефтегазовых трубопроводов в поле полиуретаны приобретают все большее значение благодаря своему быстрому отверждению (даже при низких температурах) и исключительным физико-механическим свойствам. Очевидно, соотношение цена/качество является ключевым фактором успеха на рынке окраски труб, для которого характерна жесткая конкуренция. Длинный перечень всех желаемых характеристик покрытия для труб приведен в стандарте NACE (Национальной ассоциации инженеров-коррозионистов) RP 0169 «Рекомендованные методы контроля внешней коррозии подземных или подводных трубопроводов». Подробные требования к характеристикам полиуретановых покрытий для труб описаны в европейском стандарте EN 10290 (издание 5/1999) «Стальные трубы и фитинги для сухопутных и морских трубопроводов. Наружные покрытия на основе жидких полиуретановых и полиуретан-модифицированных связующих».
Большинство широко известных строительных блоков полиуретановых покрытий для труб без растворителей — это ароматические полиизоцианаты на основе МДИ. Типичное содержание NCO-групп в полимерном МДИ составляет примерно 31%. Используя такие продукты, можно получить объемные соотношения полиольного компонента и отвердителя от, например, 2,5:1 до 4:1. Более новые рецептуры основаны на преполимерах, о которых будет рассказано ниже.
Большинство широко известных полиолов основаны на оксиде пропилена. Такие продукты могут иметь содержание OH-групп примерно от 1 до 18% и функциональность от 2 до 4. Для тонкой настройки свойств в рецептурах покрытий для труб, как правило, используются два и более полиола.
Различные полиизоцианаты, преполимеры и полиолы составляют своего рода «конструктор» для разработчика рецептуры, позволяя оптимизировать свойства покрытия и рабочую вязкость. Внутренний загущающий эффект ПУ систем можно создать путем образования мочевинных групп во время нанесения покрытия, что помогает предотвратить стекание с вертикальной поверхности и позволяет получить высокую толщину покрытия за один проход без увеличения рабочей вязкости. Поэтому ПУ системы могут выполнить заявленное требование толщины сухого слоя от 500 мкм (минимум) до 5000 мкм (и более).
Стандартные ПУ системы высыхают до отлипа примерно за 60 мин при 20 °C или за 100 мин при 5 °C. Время сквозного отверждения может изменяться примерно от 50 мин до 4 ч при 20 °C, в то время
как жизнеспособность может составлять несколько минут. Регулировка времени отверждения позволяет экономить время и деньги подрядчика, особенно при полевом нанесении, так как ускоряет весь процесс ремонта.
С химической точки зрения, реакционную способность ПУ системы легко контролировать путем введения подходящего катализатора. При этом химическая структура и конечные характеристики практически не зависят от используемого катализатора. Примерно 90% конечной твердости (по Шору D) достигается уже примерно через 4 ч, что делает эти рецептуры пригодными для полевого нанесения. Более того, две рецептуры достигают твердости по Шору D, равной 50 и 60, соответственно, уже через 5 минут, что позволяет применять их для нанесения на заводе.
Наиболее важными техническими характеристиками покрытий для нефтегазовых труб являются физико-механические свойства (твердость и эластичность пленки), а также адгезия и стойкость (по отношению к химикатам и растворителям), обусловливающие отличные антикоррозионные свойства. При сравнении жидких полиуретановых и жидких эпоксидных систем, не содержащих растворителей, наблюдается следующая тенденция: ударная прочность при данной твердости по Шору D (обычно лежащей в районе 75) выше у полиуретана.
Хорошая ударная прочность является преимуществом, поскольку транспортировка труб к месту монтажа и укладка их в землю создают нагрузку на покрытие. Удлинение покрытия при разрыве важно при изгибе окрашенных труб в поле и для компенсации температурных колебаний в регионах с холодным климатом. Кроме того, для противодействия так называемым почвенным нагрузкам важна высокая абразивная стойкость. Хорошая ударная прочность и эластичность обусловлены особым строением полиуретана: наличием жестких сегментов (образованных уретановыми и мочевинными группами, связанными между собой водородными связями) и гибких сегментов (образованных цепочками полиолов). Данный физический эффект, присущий полиуретановым системам, помогает покрытиям противостоять, к примеру, долговременным механическим нагрузкам, известным как проблема ползучести на холоду.
Физико-механические свойства можно изменять, варьируя соотношение жестких и гибких сегментов, молекулярную массу и плотность сшивки отвержденного покрытия, поэтому можно создать различные ПУ покрытия с физическими свойствами, варьирующимися от мягких/пластичных до твердых/жестких и даже хрупких.
Очевидно, что можно создать покрытия с удлинением при разрыве, варьирующимся от 5 и до 130%, при твердости по Шору D между 60 и 70. Предразрывное удлинение стандартных ПУ покрытий для труб лежит в диапазоне 10–20±5%.
Кроме вышесказанного, покрытия для труб должны обладать определенной стойкостью к катодному отслаиванию. Тест катодного отслаивания (КО) используется для оценки поведения поврежденного покрытия в типичных условиях: постоянный ток (имитирующий действующую катодную защиту), температура (соответствующая температуре эксплуатации покрытия) и раствор соли (имитирующий грунтовые воды).
В мировой нефтегазовой промышленности существуют различные методики испытаний и разные требования к напряжению, температуре, концентрации соли и продолжительности испытания. Наиболее часто применяющиеся методики основаны на стандартах ASTM G 8 «Катодное отслаивание покрытий для труб» и ASTM G 42 «Катодное отслаивание при повышенных температурах». Более высокая плотность сшивки и более гидрофобный характер 2К ПУ покрытия приводят к более низкой водопроницаемости и более высокой термостойкости в условиях катодной защиты. Кроме того, значительное влияние на адгезию и результаты теста катодного отслаивания оказывает подготовка поверхности, особенно шероховатость после пескоструйной обработки.
Новые строительные блоки жестких ПУ покрытий для труб
Многие эксперты в нефтегазовой отрасли признают преимущества многообразной химии полиуретана в покрытиях, удовлетворяющих требованиям спецификаций и пригодных для ремонта трубопроводов, окраски монтажных стыков и новых труб. Одним из преимуществ является экономия времени и финансов при окраске труб и монтажных стыков в поле — сокращение затрат на инспектирование (например, за счет низкой пористости) и засыпка траншеи уже через несколько часов после окраски. При окраске на заводе требуется лишь предварительный подогрев труб (примерно до 50 °C), так как 2К ПУ покрытия быстро отверждаются и при комнатной температуре без ограничений по толщине слоя и диаметру трубы. Более того, трубы можно обрабатывать сразу же после окраски.Жесткие 2К ПУ покрытия для труб без растворителей обладают уже довольно высокими характеристиками стандартных 2К ПУ систем. Однако благодаря их химическому составу и обусловленной им трехмерной сшитой сети, такие продукты имеют преимущества по антикоррозионным свойствам, стойкости к катодному отслаиванию при повышенных температурах (>80 °C), адгезии и водопоглощению. Позволяя смешивать компоненты в соотношении 1:1 по объему, такие системы более надежны по отношению к незначительным изменениям настроек напылительного оборудования (не всегда заметным сразу), что приводит к большей стабильности свойств покрытия.
Требования рынка к новым строительным блокам для современных 2К ПУ покрытий можно сформулировать следующим образом:
- короткое время высыхания ---> ускорение процесса ремонта = экономия времени;
- короткое время отверждения ---> короче время до засыпки = экономия времени и денег;
- один слой, прямо по металлу ---> не нужен грунт = экономия времени;
- долговечность в жестких условиях (соленая вода, высокий уровень грунтовых вод);
- хорошая стойкость к катодному отслаиванию;
- хорошая ударная прочность;
- легкость в работе ---> простое соотношение компонентов = сокращение ошибок;
- только одна система покрытия (в поле необходимы лишь 2 компонента).
Вышеперечисленные условия способствовали усовершенствованию уже хорошо известных полиуретановых сырьевых компонентов, хорошо зарекомендовавших себя в течение десятилетий:
- скрининг подходящих строительных блоков;
- выбор наилучших кандидатов для расширенных испытаний (проверка антикоррозионных свойств, адгезии, пористости, скорости отверждения и т.д.);
- разработка стартовых рецептур (для их испытания);
- создание физико-механического и реологического профиля;
- выработка простых соотношений компонентов.
Результатом разработок стал класс продуктов, называемых жесткими или структурными, на основе новых полиолов и полиизоцианатов. Выбирая данные продукты, можно создавать жесткие покрытия с простым соотношением компонентов — 1:1 и 2:1 по объему.
Ниже перечислены характеристики отвержденного покрытия на основе лабораторной рецептуры:
- объемное соотношение — 1:1;
- сушка до отлипа при 23 °C (1000 мкм) — около 20 мин;
- жизнеспособность — около 180 с (при комнатной температуре);
- ударная прочность — около 16 Дж (при толщине слоя 1,5 мм);
- адгезия — около 13 МПа (при комнатной температуре);
- твердость по Шору D — около 80 (жесткое, но не хрупкое покрытие);
- соляной туман — без изменений (через 42 суток);
- гидростат — без изменений (через 42 суток);
- тест КО (15 суток при 60 °C) — инфильтрация около 2 мм (согласно ASTM G 42);
- тест КО (15 суток при 80 °C) — инфильтрация около 3 мм (согласно ASTM G 42);
- тест КО (15 суток при 80 °C) — инфильтрация около 3 мм (согласно T/SP/CW/6, часть 1);
- тест КО (15 суток при 95 °C) — инфильтрация около 5 мм (согласно T/SP/CW/6, часть 1).
Несколько испытаний катодного отслаивания были проведены при повышенных температурах и с различным качеством подготовки стальной поверхности. Тест проводился независимым институтом Exova, в лаборатории Bayer в г. Леверкузен, Германия. Жесткое ПУ покрытие показывает очень хороший результат по адгезии и инфильтрации даже при шероховатости поверхности лишь около 50 и даже 30 мкм (обычно требуется 80–120 мкм, в зависимости от стандарта).
EXOVA: «По окончании испытания было невозможно отделить покрытие ножом — лезвие сломалось дважды, поэтому мы сделали 6 надрезов на расстоянии примерно 10 мм от повреждения и удалили покрытие при помощи молотка и стамески». Удлинение новой системы при разрыве не превышает 5%, что означает, что данное покрытие очень жесткое, однако оно не хрупкое (испытание ударной прочности проводил институт Exova).
Так как целью было ускорить весь процесс ремонта, нам удалось сократить время от нанесения покрытия до засыпки трубопровода. Развитие твердости по Шору является хорошим индикатором отверждения покрытия. Данные показали, что примерно 90% конечной твердости достигается уже через 3 ч. После успешного испытания лабораторной рецептуры AWI 012-42-C специалистами нефтегазовой компании в Саудовской Аравии были проведены два полевых испытания. Первое (AWI 012-88-2) проводили в условиях сухого грунта, а второе (MMTB 238) — в условиях влажного грунта. Оба испытания увенчались успехом. Для нас наибольший интерес представляла эффективность покрытия во влажных условиях. Через 15 месяцев эксплуатации во влажном грунте с высоким содержанием солей трубопровод откопали, и жесткое ПУ покрытие было проинспектировано специалистами нефтегазовой компании. Покрытие было в отличном состоянии, не имело дефектов, пузырей, следов ржавчины, отслаивания и т.д. Этот отличный результат позволяет сравнить свойства различных не содержащих растворителей ароматических 2К ПУ покрытий, поскольку важно выбрать «правильное» покрытие, удовлетворяющее всем требованиям и подходящее для разных областей применения (например, эксплуатация ниже или выше уровня грунтовых вод, температура эксплуатации менее 70 °C, выше 80 °C, 100 °C и т.д.).
Существует влияние плотности сшивки отвержденного покрытия на его свойства. Отвержденное покрытие на основе жесткого ПУ очень компактное благодаря очень высокой плотности сшивки, что приводит к очень хорошей стойкости к катодному отслаиванию при температурах 80–95 °C. Ударная прочность может быть более 8 Дж/мм (при комнатной температуре), хотя твердость по Шору D составляет от 75 до 85 (рецептура MMTB 238 показывает значение около 16 Дж/мм при твердости по Шору D около 80). Такая плотная пленка обладает намного более низким водопоглощением по сравнению со стандартной системой, что улучшает антикоррозионные свойства. Удлинение при разрыве составляет менее 10% (часто около 3%), что может ограничить возможность изгиба новых окрашенных труб в полевых условиях при монтаже трубопровода. Поэтому в данном случае лучше вначале изогнуть трубу, а затем нанести покрытие. Подобный материал подходит для жестких условий эксплуатации, таких как высокий уровень грунтовых вод, покрывающий трубопровод, и/или высокие температуры эксплуатации (≥80 °C). Это подтвердили результаты испытания системы MMTB 238 – особенно учитывая, что траншея была засыпана уже через 3 ч после нанесения покрытия, обычно время до засыпки составляет от 8 до 24 ч.
Кроме того, MMTB 238 соответствует и нескольким требованиям международного «эпоксидного» стандарта EN 10289 «Стальные трубы и фитинги для подземных и подводных трубопроводов. Наружные покрытия на основе жидких эпоксидных и эпоксид-модифицированных связующих».
Стандартные системы для окраски труб существуют на рынке уже в течение десятилетий (в том числе для чугунных труб) и соответствуют требованиям международного стандарта EN 10290 «Стальные трубы и фитинги для подземных и подводных трубопроводов. Наружные покрытия на основе жидких полиуретановых и полиуретанмодифицированных связующих». Такие покрытия обычно применяются для трубопроводов с температурами эксплуатации до 60 °C (в зависимости от рецептуры и выше). Для регионов с холодным климатом жесткая ПУ система может быть лучшим выбором, чтобы противостоять вечной мерзлоте.
Эластомерный тип покрытия не подойдет в качестве однослойного покрытия по металлу для высоких температур эксплуатации, так как плотность сшивки у данного покрытия ниже по сравнению с другими, что отрицательно влияет на антикоррозионные свойства и стойкость к катодному отслаиванию.
Заключение
- ПУ — универсальный класс продуктов, свойства которых можно менять в широком диапазоне;- описан процесс разработки новых строительных блоков для жестких 2К ПУ систем;
- жесткие ПУ как инновационный класс связующих доказали свою работоспособность в суровых условиях эксплуатации;
- жесткие ПУ обладают преимуществами там, где важны высокое качество и эффективность.
Так как процесс оценки технологии жестких 2К ПУ покрытий увенчался успехом и эффективность таких систем была подтверждена на практике в условиях влажного грунта, нефтегазовая компания собирается внедрить данную технологию в качестве альтернативной системы для окраски труб.
По материалам журнала «ЛКМ Лакокрасочные материалы и их применение»
Другие публикации
Рынок низкоэмиссионных лакокрасочных покрытий
Пройдя череду серьезных регулирующих нововведений, покупатели красок и покрытий осознали все преимущества использования «зеленых» материалов. В то же время движение...
03.09.2014
Тенденция роста мировых цен на сырье для ЛКМ
22.05.2014
Производство ЛКМ в России в 2012 году
22.02.2013